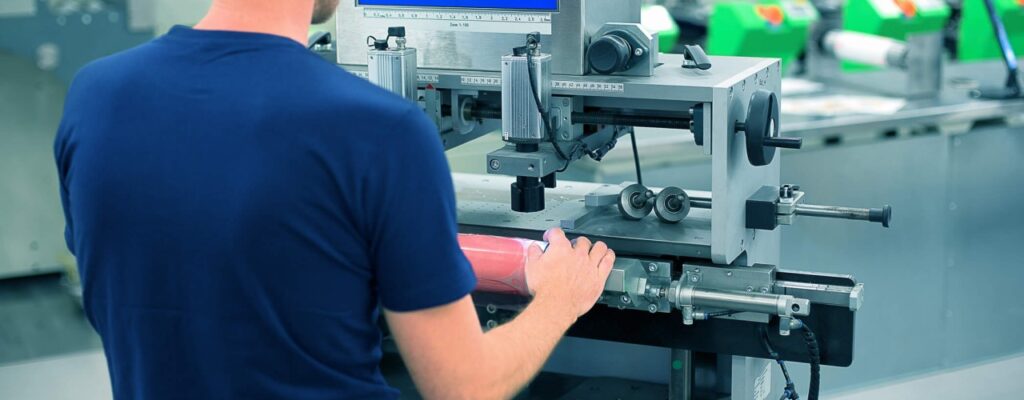
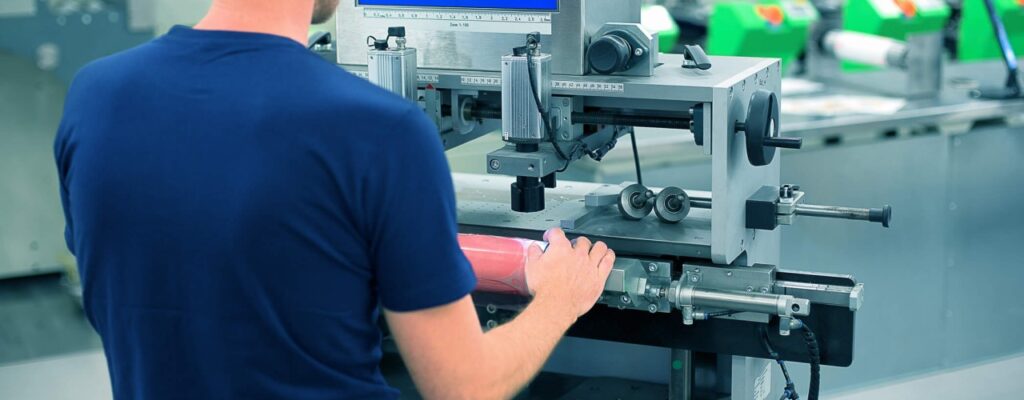
Photopolymer plates are light-sensitive printing plates used in relief printing techniques like letterpress and flexography. When exposed to UV light through a negative film, the image areas harden while unexposed areas wash away. This creates a raised surface ideal for transferring ink with precision.
For designers working with digital artwork, photopolymer plates offer a dependable and efficient bridge between traditional letterpress and modern digital workflows. At Metallic Elephant, we’ve worked with these plates across countless jobs. They hold up where it counts.
How are photopolymer plates made step by step?
Turning a digital design into a finished plate demands precision and care at each stage. Here’s how it’s done professionally:
- Generate a dense negative from your final vector file. The black areas must be fully opaque.
- Place the film directly onto an unexposed photopolymer plate.
- Use a vacuum frame to eliminate air gaps and maintain contact during exposure.
- Expose the plate to UV light – this hardens the image area.
- Gently wash away unexposed areas with a soft brush in circular motions.
- Dry thoroughly, then post-cure under UV to stabilise the plate.
Skipping steps like weak film or underexposure can lead to compromised results. At Metallic Elephant, this process is fine-tuned to deliver consistent, production-ready plates.
What artwork works best for photopolymer printing?
Not all designs suit this process. Based on our experience:
- High-contrast vector files yield the cleanest results.
- Avoid greyscale or gradient elements – they won’t convert well to relief.
- Maintain a minimum line weight of 0.5pt.
When these guidelines are followed, plates hold up under impression without breakage. On soft or textured stock, we recommend testing line weight and pressure to prevent fill-in.
Which materials are best matched with photopolymer printing?
Material choice directly affects your result. We’ve had the most success with:
- Uncoated, cotton-based stocks – ideal for deep, crisp impressions.
- Lightly textured card – visually appealing with some ink control adjustments.
- Handmade paper – effective but variable, always run a test.
Avoid glossy or coated stocks unless you’re confident in your setup. Even the best-made plates won’t overcome incompatible materials.
How durable are photopolymer plates?
With careful handling, photopolymer plates can be reused for multiple runs. Here’s what we recommend:
- Store flat in light-proof sleeves.
- Never stack plates or apply pressure.
- Clean using mild, non-abrasive solutions.
We frequently revisit plates for repeat orders and proofs but always check the edges and fine details before reusing.
Where are photopolymer plates commonly used?
From our client base, we’ve seen photopolymer used in:
- Short-run letterpress projects like invitations and stationery.
- Packaging prototypes and trial production.
- Rapid-label production lines.
- Artist studios merging hand-finished detail with digital precision.
Their speed and consistency make them a go-to for professionals who need reliability without excess setup.
Who typically uses this technique?
We work with:
- Independent printmakers.
- Small batch packaging teams.
- Graphic designers preparing artwork for plate making.
- Mixed-media artists testing new applications.
These users value accuracy, turnaround speed, and predictable results – photopolymer offers all three.
How do photopolymer plates compare to traditional methods?
Compared to magnesium or metal plates, photopolymer brings several advantages:
- Safer, cleaner handling.
- Faster turnaround from design to plate.
- Easier setup from digital files.
- Minimal waste and lower overhead.
We’ve helped many studios switch to photopolymer once they realise how much time and material they save.
What are the key benefits in practical use?
Based on production experience, benefits include:
- Easy integration with Illustrator or CAD designs.
- Reliable for moderate print volumes.
- Compact and durable for tight studio spaces.
- Less prep time, fewer errors.
They suit both boutique shops and growing businesses managing multiple design styles.
How to get consistent, high-quality results
To get the most from your plates:
- Always use high-quality vector art.
- Ensure film contact is tight and dust-free.
- Wash out with care and control.
- Complete the post-cure without skipping.
- Fine-tune your packing to avoid crushing details.
These steps matter. We’ve seen top-tier results from clients who follow them without compromise.
Are there known limitations?
Yes, and knowing them is key:
- Edge detail can soften with reuse.
- Insufficient exposure reduces relief quality.
- Fine lines are vulnerable in the washout stage.
We advise testing fine features and reviewing plate condition before major runs.
How does photopolymer integrate with letterpress?
Photopolymer plate technology has modernised the letterpress process without removing its character. At Metallic Elephant, we’ve seen a growing number of clients move away from metal typesetting or etched magnesium to take advantage of photopolymer plates‘ speed and flexibility.
Our letterpress solutions allow printers to pair traditional hand-fed presses with new-age plates that deliver accurate registration and cleaner impressions. Whether you run a classic platen press or a modern cylinder model, we can help you choose the right plate thickness, adhesive base, and artwork setup for best results.
Is this process right for your next job?
If your projects require detail, repeatability, and fast turnaround, photopolymer is a smart option. We’ve supported hundreds of businesses shifting to this method with measurable success.
Get advice from people who’ve done it
Want an expert view on your artwork or need help planning your next print job? Contact our team. We know what works because we’ve used it in the field time after time.